It’s important to consider the differences between CNC and CMM when deciding which kind of machine to use for a project.
Choosing the wrong one can lead to a faulty product that won’t meet your needs – and that’s not something anyone wants!
With the right information, you can pick the right machine for your needs.
I’ve done the research for you and broken down the differences between CNC and CMM machines so you can make an informed decision.
Let’s get into the details!
Key Takeaways
- CMM machines are used to inspect parts and assemblies, ensuring that meet engineering specifications and tolerances.
- CNC machines use cutting tools to create precise components on programmed instructions.
- Both technologies play a critical role in manufacturing processes, but the choice of CMM vs. CNC depends on specific requirements
What is a CNC Machine?
A CNC (Computer Numerical Control) machine is a modern manufacturing technology that has revolutionized industries ranging from automotive and aerospace to medical and consumer goods.
It is a highly advanced machining device that uses computerized software programs to control the movement, speed, and precision of cutting tools to produce high-quality, complex, and accurate components and parts.
CNC machines are capable of creating parts with high precision and accuracy, even beyond what is possible for even the most seasoned machinist to achieve manually.
The technology of CNC machines is based on digital instructions, inputted through a computer program, which drives the machine to perform precise and repeatable movements.
The program controls the cutting movements, the speed and feeds of the cutting tools, and other variables important for the production of an accurately machined part.
Incorporating modern IT Solutions for Manufacturing can further enhance these benefits by integrating advanced software, automation systems, and real-time monitoring into your CNC workflows. These solutions help manufacturers optimize performance, reduce downtime, and maintain tighter control over production quality.
CNC machines have numerous advantages over traditional manual machining, including the following:
- Precision
- Accuracy
- Repeatability
- Speed
- Flexibility
These advances in technology are expanding industries such as manufacturing in a big way.
What Does a CNC Machine Do?
CNC machines are used to produce precise and complex parts.
They can be used to create a variety of components, including:
- Medical devices
- Automobile parts
- Aerospace components
- Electronics
- Consumer products
The technology is capable of producing parts with high precision, accuracy, and repeatability which would otherwise be impossible for even the most experienced machinist to achieve manually.
How Does a CNC Machine Work?
A CNC machine works by inputting a program into the computer software.
This program is then translated into instructions that control the movements of the cutting tools and other variables, such as speed and feeds.
The machine then moves according to these instructions to accurately produce high-quality components with repeatable precision.
What are the Advantages of a CNC Machine?
There are numerous advantages to using a CNC machine, including the following:
- High precision and accuracy
- Repeatability
- Speed
- Flexibility
- Consistency
- Reduced manufacturing time
Types of CNC
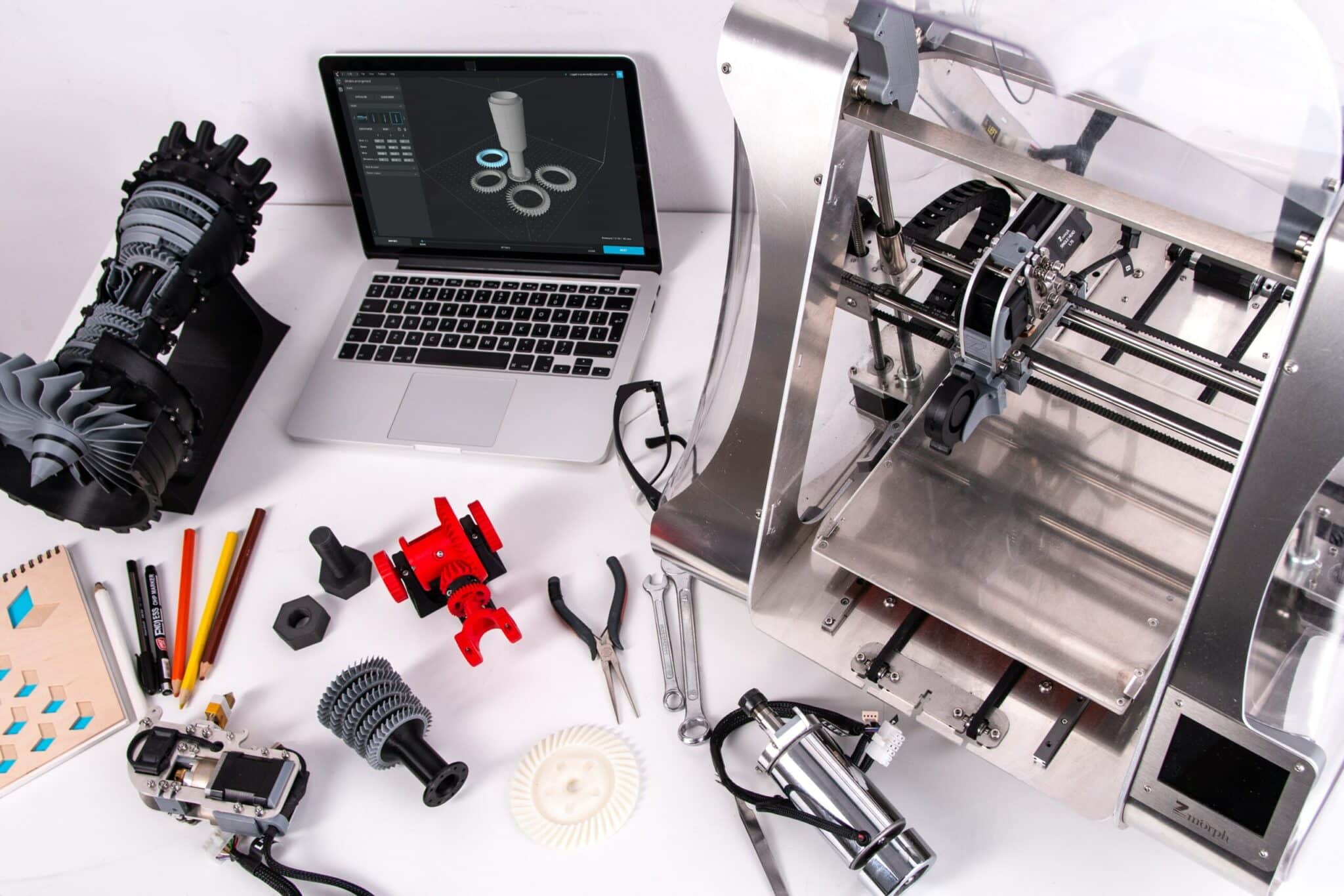
There are several different types of CNC (Computer Numerical Control) machines, each catering to specific manufacturing requirements.
Choosing the right CNC machine for your needs is essential to ensure the quality and accuracy of your finished product.
The most common types include:
- Milling machines
- Turning machines
- Plasma cutters
Milling machines are used to cut and shape various materials such as metal, plastic, and wood. These machines are incredibly versatile, offering high precision and accuracy.
Turning machines are used to create cylindrical parts, and they can produce intricate designs with relative ease.
Plasma cutters, on the other hand, are used to cut metals using a high-velocity jet of ionized gas. They offer speed, efficiency, and quality cuts, making them prevalent in the metalworking industry.
In addition to these, there are several other types of CNC machines such as laser cutters, water jet cutters, and even 3D printers that use CNC technology to produce intricate designs and parts with high precision and speed.
What is a CMM?
A CMM or Coordinate Measuring Machine is a device used to measure the physical geometries of objects.
A CMM is considered the most versatile measuring tool in a lot of industries, allowing for the most accurate measurement of a part’s geometry.
What Does a CMM Machine Do?
CMM machines can be used to inspect a wide range of objects, from small parts to large assemblies.
The three-dimensional data collected by the machine is then evaluated and analyzed, allowing for precise dimensional and geometrical measurements to be taken.
This data is then used to ensure that parts and assemblies meet engineering specifications and tolerances.
CMM machines are typically used in industries where precision and accuracy are critical such as:
- Aerospace
- Automotive
- Medical device manufacturing
With the advances in technology, modern CMM machines are equipped with various sensors, which allow for non-contact measurement and increased speed and efficiency of the inspection process.
Overall, the CMM machine plays a crucial role in ensuring the quality and consistency of manufactured parts, making it an essential tool for modern manufacturing processes.
How Does a CMM Machine Work?
A CMM machine works by moving a probe across the surface of an object and collecting x, y, and z coordinates which are then used to determine the shape and size of that object.
The machine is usually computer-controlled, allowing for precise movement of the probe along predetermined paths. This allows for accurate measurements to be taken quickly.
What are the Advantages of a CMM?
The main advantages of using a CMM include:
- Accuracy
- Precision
- Speed
- Repeatability
Types of CMM
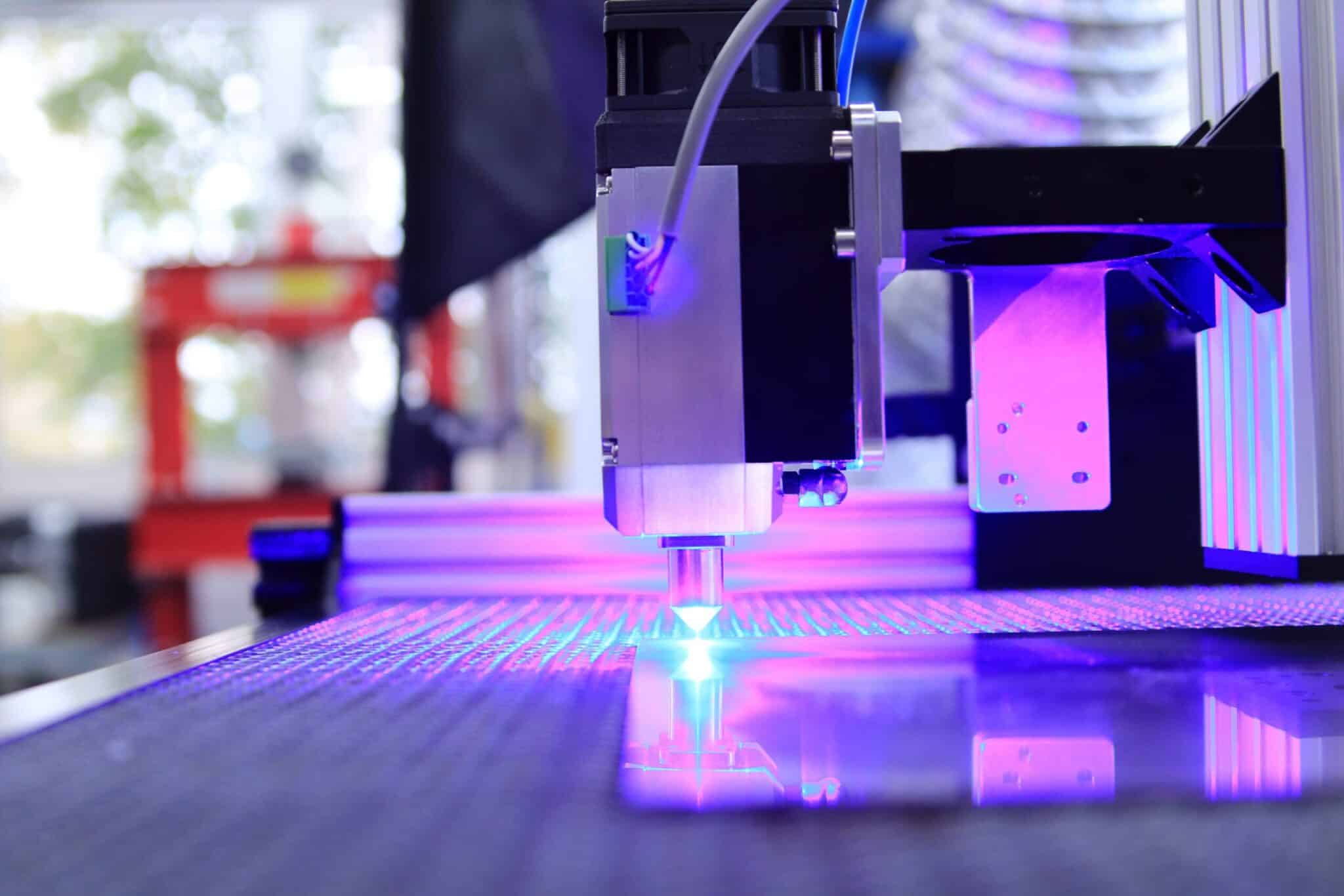
Just like with CNC machines, there are several types of CMM machines designed to cater to specific requirements. The most common type is the bridge-type CMM which is usually used in large parts inspection applications.
Other types include gantry-style CMMs, horizontal arm CMMs, and 3D scanners. Each machine has its advantages and disadvantages, so it’s important to choose the one that best suits your needs.
CMM vs. CNC: What’s the Difference?
CMM and CNC are both manufacturing technologies that have a significant impact on production processes. CMMs are used to determine the geometrical characteristics of an object, including its shape, size, and location.
As we’ve discussed, CMMs use high-precision probes to capture exact measurements of the object, making it an ideal tool for quality control and ensuring consistent products.
In contrast, CNC machining is a process of creating precise components by programming computerized instructions into machine tools.
CNC machines use cutting tools to shape materials based on the programmed instructions, providing a high level of accuracy and precision.
While CMM and CNC technologies differ in their functionality, they both play a critical role in ensuring that manufacturing processes meet the highest standards of quality and efficiency.
CMM Vs. CNC Conclusion
Ultimately, the choice of CMM vs. CNC depends on the specific requirements of your manufacturing process.
CNC machines are perfect for creating precise components with high accuracy, while CMMs offer unparalleled control over dimensional and geometrical measurements.
To get the best results from both technologies, it’s important to choose the right one for your specific needs. Do you have any questions? Let us know in the comments below!
A: It depends on the specific requirements of your application. Both technologies offer high levels of accuracy and precision, but they are used in different ways in manufacturing processes.
A: There are several types of CMM machines available, such as bridge-type CMMs, gantry-style CMMs, horizontal arm CMMs, and 3D scanners. Each has its advantages and disadvantages, so it’s important to choose the one that best suits your needs.
A: The primary difference between CMM and CNC is in their functionality. CNC machines are used to create precise components by programming computerized instructions into machine tools, while CMMs are used to determine the geometrical characteristics of an object, including its shape, size, and location.