There are currently over 2 million registered companies in India, while only 1.1 million are active. Shockingly, only 7 of them could make it to Fortune 500 in 2020. On the other hand, the US has over 33 million companies registered with 121 under Fortune 500 in 2020.
Have you ever wondered why there is so much disparity between India and the US? And why only a handful of companies make it big even in the US? Also, only 25% of today’s total businesses are expected to survive for the next 100 years. What tricks of the trade play a role that makes all the difference? Which businesses succeed to come under Fortune 500, and why do only a minuscule number last 100 years?
The answer to all these questions points to one common factor: the ‘Process Improvement’ of any business. It plays a significant role, and the efficiency for the overall success of a business depends on it. Topmost companies worldwide have consistently been applying effective Six Sigma tools for the past 3 decades to improve various internal and external processes. The senior-most positions of these firms are filled with professionals who are proficient Six Sigma practitioners.
Why Six Sigma? Why Lean?
Six Sigma is a series of tools and methods that examine the root causes behind slow business processes, evaluate wastages involved, and reduce errors and risks. A data-driven problem-solving approach is essentially used to improve the process by streamlining operations, reducing variation, and assuring product quality.
Lean is a systematic approach making quality a quantifiable statistic. Its end goal is to eliminate wastes in the business processes by scientifically studying them.
What is waste? Regularly waiting for product shipments is a waste. Products sitting in storage until needed are a waste. Processes taking weeks to be actioned are a waste. Waste is, fundamentally, anything that isn’t adding value or benefitting the bottom line.
Thus, Six Sigma improves the process’s outcome while Lean cleans up actions between the value addition processes. The synchronization of the two ensures the operations’ smooth running and no downtime in the business process. Thereby, it fosters business process management, eliminates waste and inefficiencies, improves the quality of product and service to meet specific client needs, and optimizes the process through Lean Six Sigma.
Hence, the combination of both is a perfect tool for customer satisfaction and retention, employee morale boost, improved profitability, cost and time-delay reduction, and sustaining quality control by reducing the defects to less than 3.4 per million output units.
5 Tools to Enhance the Process
The process improvement endeavor requires the statistical analysis of the DMAIC tools to determine, measure, analyze, improve, and control. This is done to enhance the process’s competencies with better usage of resources to achieve maximization and improved quality standards.
It entails utilizing root-cause analysis for making better business decisions to expand the chances of achieving successful results.
The following five tools are necessary for the execution roadmap for process improvement:
1. Flowcharting
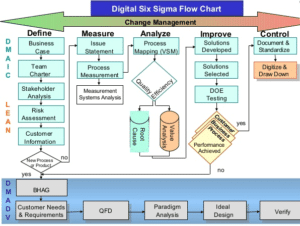
Flowcharting is one of the most effective instruments used to document and identify the various processes and structures in any business organization. This powerful tool helps break down the entire process into actions and steps to define reasonable relationships amongst the elements involved. This is done to achieve a better comprehension of the work efforts engaged in process undertakings.
Thus, flowcharting is a continuous task utilized throughout the introduction, development, and delivery of a project. It helps to generate results without stoppages, wastes, scrap, and backflows. Its design aims to reduce waste within the process by eliminating the primary cause of waste. This is the most crucial aspect of the process, which is reached via the Six Sigma method.
For example, encoding in the computer system can be characterized into a sequential order using flowcharting tools. The graphical use of symbols such as circles, boxes, diamonds, and other forms of shape connected via lines represents the process’s direction.
Symbolizing every step helps communicate, clarify, and reduce errors within a process in an organization.
2. Process Baselining and Evaluations
When baselining and assessing the performance of a process in comparison with other parallel processes, four instruments are used, namely:
-
Building Baseline:
The first step is to create and define a clear business process baseline. This effort must cover all aspects of the process against which a basis would be created. By doing so, a better description of current procedures in the organization can be stated, and thus, the improvement areas could be defined. Therefore, creating a baseline for the project which is predictive and focused is the foremost task.
-
Classifying Baseline:
In this step, all the other organizations are determined against which performance evaluation would be made. Different factors must be considered for this decision, such as comparing the process performance to a prominent company within the same industry or comparing it with a similar culture.
-
Carry out Comparison:
Robust evaluations should be made based on statistics. For example, developing a hypothesis of ‘equality of means’ for the process’s output response.
-
Ascertain the Baseline Differences:
This step is of utmost importance as identifying the differences in the performance and the causes behind them are ascertained. The significance is that it helps understand the lacking in the process and the suitable adjustments that need to be made.
3. Hypothesis Testing
Hypothesis testing includes two sets of hypotheses – Null hypothesis and Alternative hypothesis. A Null hypothesis shows equality between outputs of the two processes while an Alternative hypothesis shows a non-equality. While holding a hypothesis test, a decision is made about rejecting or not rejecting the null hypothesis through regression analysis.
This may also involve a risk of making a mistake for which mistake-proofing comes into the picture. There are many formats of Hypothesis testing. However, selecting the most suitable for the business process is critical.
4. Value-Stream Mapping
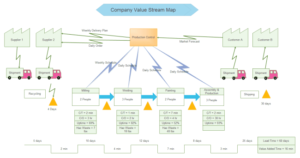
This tool outlines the flow of necessary steps, information, and materials in an end-to-end process. This is done for prompt project delivery and completion by optimizing and improving the flow in the organization. The focus is to envision information such as error rate, time-period, and unnecessary delays to bring a quality product to the customer.
The three parts of value-stream mapping — the process map, the timeline, and the information flow — help visualize the current state. A future state can be proposed to streamline the process and reduce waste of inventory, transport, overproduction, defects, motion, waiting, and over-processing. The process map entails each step taken in the production process through which the timeline is derived. The timeline summarizes and reviews all the data, while the information flow explains the interaction between the steps.
Three activities are discovered using value-stream mapping:
- Value-adding activities
- Value-enabling activities
- Non-value adding activities
Thus, the whole purpose is to make the processes more precise, rapid, and compact. This is done by removing wait-times and waste between consecutive steps and cutting non-value-adding activities. Thereby developing a flow from work-in-progress to standardized quality timelines.
5. Cause and Effect Analysis
The fishbone diagram in cause and effect analysis is used to brainstorm and explore all the probable causes behind a problem. The probable causes are further broken into sub-causes, and a summary of when and where the process occurs is detailed.
Thus, the cause and effect analysis approach offers a comprehensive structure for assessing the root cause. Six areas are considered for the effect:
- Materials
- Personnel
- Machine
- Measurement
- Method
- Environment
Once all the plausible causes are diagrammed, results are analyzed. A solution can become apparent at once. However, it may need further analysis and testing. In some cases, the cause may not be clear enough for historical data and its statistical analysis to check out various theories.
Conclusion
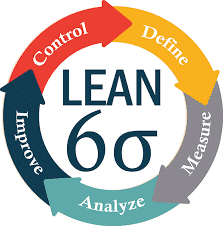
In the pandemic afflicted 2020 world, the prospects are dwindling, and staying competitive is not a piece of cake. The most successful ventures globally have applied Six Sigma tools since their first days in the industry. And Six Sigma continues to show effective and commendable results for the businesses and their process improvement endeavors.
A Six Sigma certification online is the most convenient way to gain a comprehensive understanding of Six Sigma methodologies and tools and apply them for streamlining various processes. Incorporating the five tools in process improvement will work wonders for an organization and help it emerge victorious amid the growing economic uncertainties and ever-increasing competition in the industry.
DepositPhotos – six sigma