Are you familiar with Cycle Time? If not, don’t worry – we’ve got you covered!
Cycle Time is a key metric in project management, and it’s important to understand its formula, definition, and use cases.
Having worked in business operations for the past five years, I’ve seen Cycle Time used in many different ways.
Cycle Time is a powerful tool that businesses can use to measure and analyze operational performance. In this article, I will teach you how to use Cycle Time in your operations to gain insights into efficiency and throughput.
Cycle Time Explained
So, what is Cycle Time?
In the following section, I will provide an in-depth explanation of Cycle Time and its formula, definition, and use cases.
What is Cycle Time?
At its most basic, cycle time is the elapsed time between the start and finish of a task or process. In software development, this could be the time it takes to complete a user story or bug fix or the time it takes to review and merge code changes.
The goal of measuring cycle time is to identify inefficiency and improve the speed at which businesses complete their work.
Businesses can use Cycle Time in many different ways:
- To monitor the performance of teams and processes
- To identify areas where workflows need improvement
- To help prioritize tasks and workloads
- To determine potential bottlenecks in a process
- To track progress on projects
- To increase efficiency and throughput.
Cycle time is an essential concept in software development that refers to the time it takes to complete a specific task or process.
It is often used to measure the efficiency and productivity of a team or process and can be a critical factor in determining the overall success of a project.
Cycle Time Formula
There are several ways to measure cycle time, depending on a project’s specific needs and goals.
Some common methods include:
- Tracking the elapsed time between the start and finish of a task or process.
- Measuring the number of tasks or items completed within a specific period.
- Analyzing the flow of work through the development process, including how long it takes to move from one stage to the next.
No matter which method, you must follow the cycle time formula to calculate properly.
The cycle time formula is: Cycle time = Net production time / Number of units produced.
How to Calculate Cycle Time (Example)
Let’s say you are trying to measure the cycle time for a production line.
The production line runs for 8 hours and produces 100 widgets. Using the cycle time formula, we can calculate Cycle Time as follows:
Cycle time = 8 hrs / 100 widgets = 0.08 hrs per widget
This means it takes an average of 0.08 hours to produce one widget on the production line.
Takt Time Explained
Now that you have a better understanding of Cycle Time and its formula let’s turn our attention to Takt Time – another key performance metric in production management.
What is Takt Time?
Takt time, which translates literally from German to ‘rhythm,’ is the cycle of production that a manufacturer needs to follow to meet customer demand.
Takt time is not a measure of the total time taken to complete any part of the production cycle but rather the rate at which a business must complete work to satisfy customers’ expectations.
This focus on rhythm ensures that customers receive what the business has promised them while streamlining the production process and helping companies save precious cycle time.
Takt Time Formula
Businesses use the takt time formula to calculate the rate at which they must produce products to meet customer demand.
The Takt Time formula is: Net available working time/ customer demand.
The result of this calculation is the takt time, which is expressed in units of time (e.g., minutes, hours).
How to Calculate Takt Time (Example)
Suppose a manufacturer has 30 minutes of available working time per day, and customer demand is set at 500 units. Using the takt time formula, we can calculate Takt Time as follows:
Takt time = 30 mins / 500 units = 0.06 mins per unit
This means it takes an average of 0.06 minutes to produce one unit to meet customer demand.
Lead Time Explained
Lead time is an important metric for any business that takes orders, as it helps to provide accuracy and expectations for delivery times.
Now that you know Cycle Time and Takt time, let’s look at the lead time and how it can help optimize production.
What is Lead Time?
Lead time is the total elapsed time from the moment a client orders an item to receiving the final product.
Lead time is critical in understanding how long it takes to fill an order, helping businesses assess if they are meeting customer demand.
Properly calculating cycle and lead times enables companies to accurately anticipate and plan for customer orders, resulting in improved customer service.
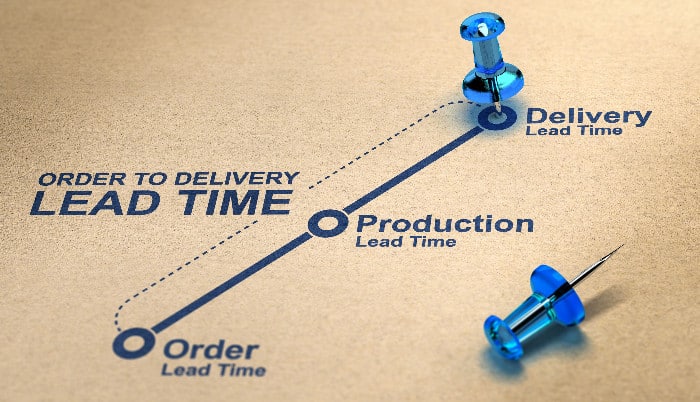
Lead Time Formula
Understanding the lead time formula is essential for any business to effectively anticipate stock needs and cycle times. This formula outlines the sum of two components, supply delay and reorder delay.
- Supply delay is the amount of time allocated between ordering a new batch of supplies and receiving them.
- Reorder delay represents the gap in cycle time that allows businesses to use existing supplies before restocking.
The Lead Time Formula is: Supply Delay + Reorder Delay.
How to Calculate Lead Time (Example)
Let’s say a widget factory needs to restock its supplies every 10 days and the estimated supply delay for each order is 5 days. Using the lead time formula, we can calculate lead time as follows:
Lead time = 5 days + 10 days = 15 days
This means it takes an average of 15 days from when a customer orders a widget until they receive it.
Cycle Time Benefits
By understanding Cycle Time, Takt Time, and Lead Time, businesses can manage their production processes more efficiently and accurately anticipate customer orders.
With this knowledge, manufacturers can ensure they meet customer demand while optimizing cycle times and minimizing lead times. Let’s look at other benefits businesses can expect from understanding cycle time.
Increased Profitability
Cycle Time is a valuable resource for businesses as it allows them to identify inefficiencies and improve production processes. This can increase profitability by reducing cycle times, eliminating waste, and increasing throughput.
By understanding Cycle Time, businesses can optimize all aspects of their production process for maximum profitability. Cycle Time is an invaluable tool for any business looking to increase its bottom line.
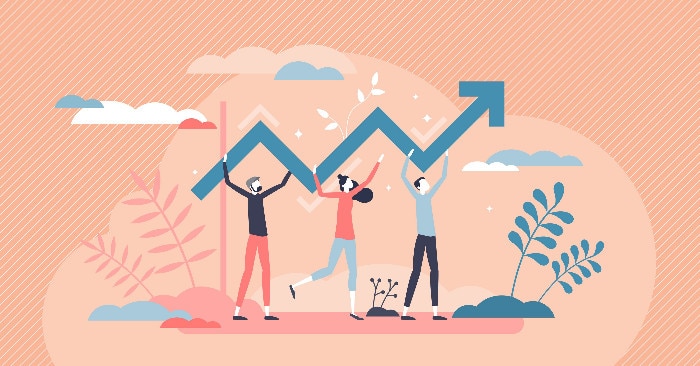
Cost Savings
By understanding Cycle Time, businesses can identify areas where they can streamline processes and reduce the number of steps involved in producing goods or services.
This eliminates unnecessary investments of time and money, ultimately saving significant production costs.
Furthermore, Cycle Time reduces lead times, which helps to reduce the cost of carrying inventory, as businesses can better anticipate customer demand.
Increased Production
Cycle Time helps to increase production as it provides businesses with an understanding of the most efficient way to produce goods or services.
Businesses can use this to optimize production processes and ensure they work at maximum efficiency, resulting in increased output and higher customer satisfaction.
Better Project Scoping
By understanding Cycle Time, businesses can gain insight into how long it takes to complete tasks and more accurately estimate the time required for production.
This enables businesses to provide better estimates of project scopes when dealing with clients, helping them allocate resources appropriately and set realistic expectations.
More Efficient Team Structure
Cycle Time helps businesses to create a more efficient team structure. By understanding Cycle Time, businesses can identify the most efficient way to divide tasks between team members and optimize their production process accordingly.
Cycle Time also aids in developing processes that are well-suited for each individual’s skill set, allowing teams to function more smoothly and efficiently.
Better Ideas for Business Spending
By calculating Cycle Time, businesses better understand their production process and how they can reduce costs.
Cycle Time enables businesses to decide where to allocate resources and invest in the most effective technologies. Cycle Time also helps inform businesses when it’s most appropriate to invest and spend money, allowing for maximum efficiency in capital expenditure.
Cycle Time Challenges
Although Cycle Time is a powerful tool for businesses, some challenges can arise when utilizing Cycle Time as part of the production process.
Prioritization with Tasks
One of the main challenges when using Cycle Time is prioritizing tasks.
Cycle Time requires careful management and decision-making to ensure they complete all tasks as efficiently as possible while meeting customer demand. This can prove difficult for businesses, as they may face conflicting objectives and limited resources.
Additionally, Cycle Time requires a detailed understanding of the production process to accurately prioritize tasks and optimize efficiency.
Distribution Channel Issues
Another challenge with Cycle Time is the potential for distribution channel issues.
- Cycle Time requires a detailed understanding of each step in the production process and how it impacts customer satisfaction.
- This can be difficult to manage, especially if businesses work with multiple distributors or third-party providers.
- As Cycle Time focuses on reducing lead times, changes in distribution channels can significantly impact Cycle Time, leading to delays and customer dissatisfaction.
To ensure the successful implementation of Cycle Time, businesses must be aware of potential distribution channel issues and take steps to minimize their impact.
Lack of Team Collaboration
A lack of team collaboration can lead to Cycle Time challenges, as Cycle Time is dependent on the effective coordination of tasks between all team members.
- Without adequate communication and collaboration between team members, businesses may not meet their Cycle Time goals, resulting in missed deadlines or inefficient production processes.
- Additionally, Cycle Time relies on accurate data gathering and analysis to effectively identify tasks and prioritize them according to customer demand, which is impossible without team collaboration.
To ensure Cycle Time is successful, businesses must ensure that all team members work together and communicate effectively.
Takt time Vs. Cycle Time
Cycle Time and Takt Time are two essential components used to assess the capabilities of a production cycle.
- Cycle time measures how quickly a business can complete a cycle of operations or processes. It gives manufacturers a good understanding of what they are capable of producing.
- Takt time calculates customer demand and is externally driven by market needs; it provides targets for cycle time that a business must meet to maintain customer satisfaction.
By understanding the distinction between cycle time and takt time, production managers can accurately assess their ability to meet the needs of their customers, accounting for necessary lead times during processing.
The simultaneous tracking and analysis of cycle and takt times can provide valuable insight for manufacturing operations planning.
Lead Time Vs. Cycle Time
Understanding the differences between cycle and lead time can be complicated as they measure different aspects of a production process.
- Cycle Time measures how quickly a manufacturing process completes once it has begun.
- Lead time encompasses all aspects leading up to and after the operation cycle, such as the time needed for materials acquisition, production processes, and customer delivery.
- Cycle Time is measured internally, while lead time sees matters from a customer perspective.
This key distinction can help manufacturers improve their lead times by examining cycle times to find areas for improvement.
By continuously monitoring these metrics and looking for opportunities to reduce cycle times, manufacturers can reduce cycle times that may impact their lead times, thus leading to greater overall efficiency.
Conclusion
Understanding Cycle Time is essential for any business looking to optimize its production process and increase profitability.
By using Cycle Time, Takt Time, and lead Time calculations, businesses can better anticipate customer demand and create a more efficient team structure.
Cycle Time enables them to make cost-effective decisions when it comes to investing in technology and resources, making it an invaluable tool for any business looking to succeed.
Now we’d like to hear from you; have Cycle Time calculations helped your business increase efficiency or identify areas of improvement? Tell us about it in the comments below!
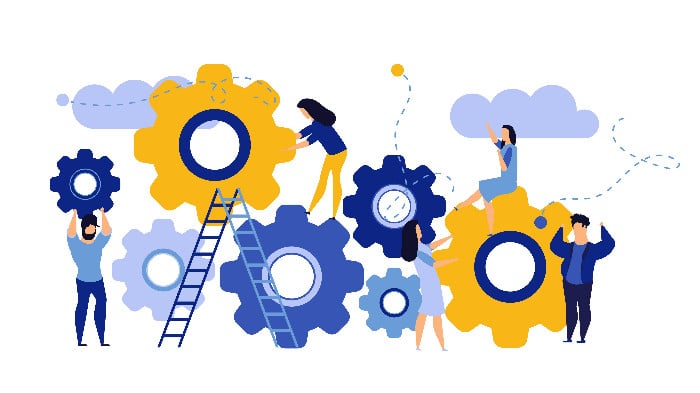
Frequently Asked Questions
The length of your cycle depends on the specific production process you are measuring. Cycle time is calculated by counting the number of days it takes to complete a single cycle, from start to finish.
Cycle Time helps businesses assess their ability to meet customer demand by understanding how quickly their production processes can complete a cycle. Cycle time metrics also provide insight into areas of improvement that can help reduce lead times and increase efficiency in the long run.
A Cycle Time Chart is a visual representation of Cycle Time metrics gathered over time. This allows businesses to track their performance, identify areas of improvement and develop strategies for increased efficiency.
The two types of cycles are Cycle Time and Lead Time. Cycle Time measures the time it takes for a production processes to complete one cycle, while Lead Time encompasses all aspects leading up to and beyond Cycle Time such as materials acquisition, production processes and delivery to customers.
No, Cycle Time and Flow Time are not the same. Cycle Time measures the time it takes to complete one cycle of a production process, while Flow Time measures the total amount of work done in a given period of time.
Yes, Cycle Time includes all aspects of the production process including setup time. Setup times are typically included in Cycle Time calculations as it is important for businesses to understand how much time each step of their production process requires.